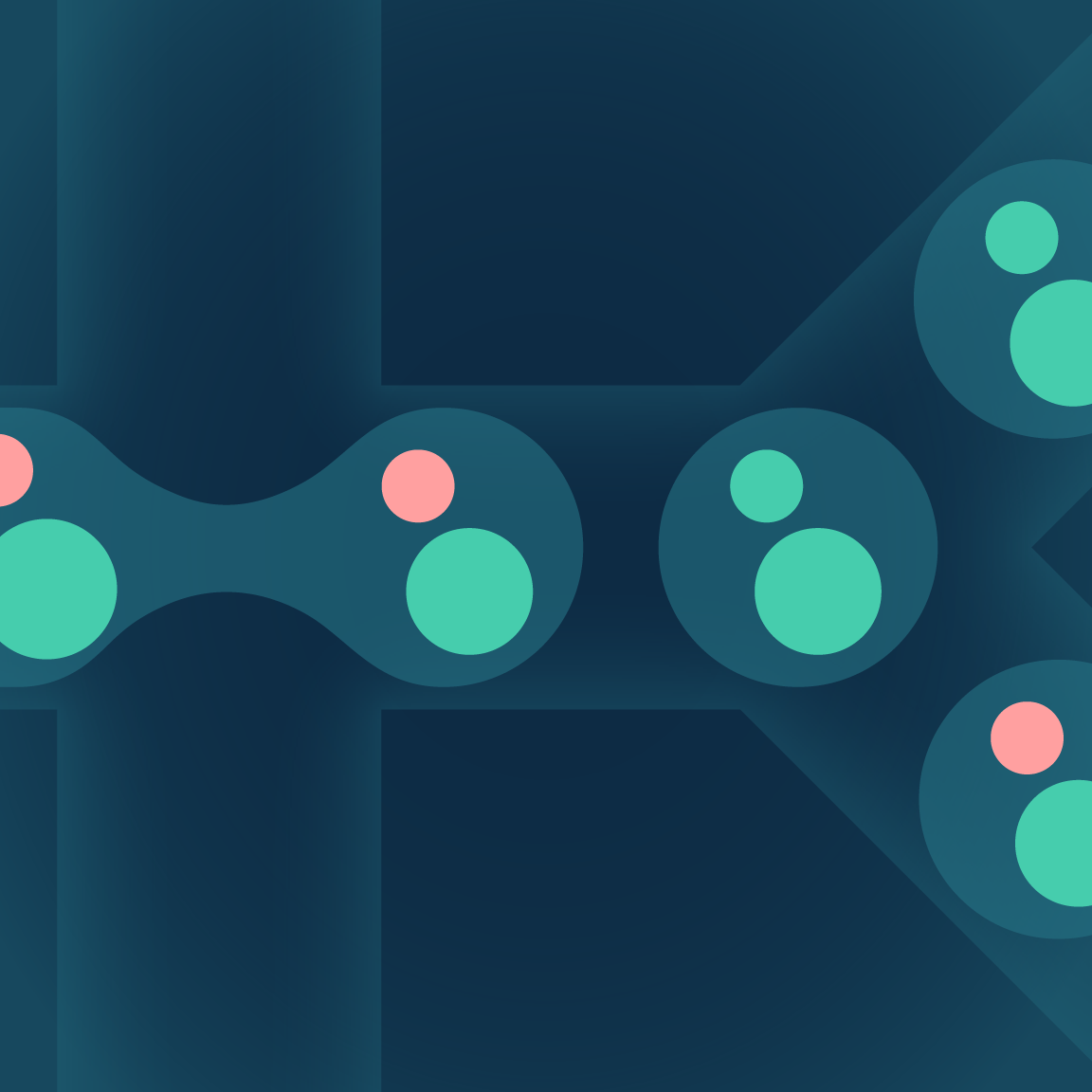
Scientific Facility for Microfabrication and Microfluidics
µFlu CF
Microfluidics is an emerging field and is finding use in various disciplines. Starting from understanding flow mechanisms, to the generation of synthetic cells with droplet-based microfluidics, continuous flow microfluidics to complex organ-on-a-chip models. The Microfluidics Core Facility (µFlu CF) aims to provide this valuable tool to every interested research group within the Alliance.
Technologies
µFlu CF supports researchers from the start by providing input on project design, production of microfluidic chips, and conducting experiments in its S1 and S2 Biosafety laboratories. The facility also offers an introduction to the microfluidic workflow, including the handling and usage of microfluidic chips. These tasks can be carried out at the facility either independently or under supervision. The facility has several instruments used for fabricating microfluidic devices ranging from 5 µm to 3 mm with different techniques. The focus is not only on the generation of PDMS-based microfluidic chips but also on the application of nested glass capillary-based devices and 3D-printed devices and structures.
Droplet-based Microfluidics
Droplet-based microfluidics is a big sub topic in microfluidics. Water-in-Oil droplets or micrometer-sized Oil-in-Water droplets can be produced on chip or by means of glass-capillary nested devices. Water-in-oil droplets are widely used to encapsulate any wanted cargo which can then be analyzed in small compartments. The droplets find applications in single cell sequencing, antibody screening, cell-cell interactions and many more because the content is restricted to the droplet size and not diluted in a bigger volume. This also allows the study of single cells without interference of surrounding cells. Another application of droplet-based microfluidics is for the production of e.g.: beads or capsules consisting of proteins and/or hydrogels. Within the µFlu CF, we prepare the microfluidic chip with the appropriate design, tailored to the project needs of the user. We further offer guidance and help in the generation process of such droplets. Further, we also generate oil-in-water droplets, which are handed to the user to be used for further experiments.
Microfabrication of Devices for cell migration
We offer fabrication services of devices for cell migration. Using photolithography allows us to generate paths and obstacles for cells to migrate through, around or even above. The image shows channels bridging two reservoirs. The channels have a height of around 10µm, while the reservoirs are 200µm high. This allows the cells to attach in the reservoirs and forces them to migrate through narrow spaces. The cells can be later collected or analyzed directly on chip. This is again just an exemplary device; the channels and reservoirs can be altered in shape, geometry and dimensions, making this a powerful tool for cell analysis. Besides cell migration, these structures can also be used to investigate cell-cell communication or other relevant questions. These are just examples for applications.
Real-Time Deformation Cytometry
The µFlu CF has access to a real-time deformation cytometer. This instrument allows for the fast and high-throughput stiffness analysis of single cells. By using narrow microfluidic channels (purchased from Zellmechanik Dresden), cells are deformed by the flow in the surrounding. Based on this deformation, the stiffness is calculated and displayed. In the figure, the green and the yellow squares show the difference between deformed and not-deformed cells.
Organ-on-Chip techniques (under development)
Given the importance of Organ-on-Chip technologies we are currently working on the fabrication of such chip systems. Combining 3D printing and lithography we are trying different methods to achieve the best result. This technique is not yet completely established within the µFluCF, nevertheless we are open for collaborations and production of such chip systems if this is of importance for projects. Please do not hesitate in contacting us in this demand.
Continuous Flow Experiments
We offer three different services that use continuous flow techniques: On-chip particle sorting, gradient on-chip, and lipidnanoparticle (LNP) generation.
On-chip particle sorting
Using a spiral chip, it is possible to introduce differently sized beads in the sample inlet and in parallel a sheath flow which forces the particles to separate over multiple rounds through the spiral. The separated particles are collected over single outlets at the end of the chip. The second image shows the particles being separated from the inner circle outwards, indicated with an arrow.
Gradient on-chip
Besides fast flow microfluidic experiments, we can also make use of the laminar flow regime at lower flow rates. Combining this with a specific geometry it is possible to generate very precise gradients on a chip. This image is just an example of a gradient chip. The more mixing units are added a more precise the gradient can be established. There are more possibilities in generating gradients on-chip, then with this design.
Lipidnanoparticles (LNPs)
It is also possible to generate LNPs by using microfluidics. By introducing turbulent flows, it is possible to mix two phases which then lead to either empty or loaded LNPs, depending on the cargo loaded in one of the continuous phases. The image shows a microfluidic bifurcating mixer. However, there are also different designs possible for the production of LNPs.
Equipment
The facility offers the following microfluidic-chip production and validation equipment as well as microfluidics equipment.
- 3D Printer (microArch S140)
- Pressure-based Flow System (Elveflow)
- Syringe Pumps (Infustek)
- Microscope Axiovert A1 (Zeiss)
- Microscope Axiolab 5 (Zeiss)
- High-Speed Camera MiniUX50 (Photron)
- CutterPlotter CE7000 (GraphTec)
- Ultra Turrax Emulsifier (IKA)
- HMDS Oven (Zeno Boldor)
- Micropipette Puller and Microforge (WPI)
- Maskless Aligner (Heidelberg Instruments)
- Spincoater (Laurell)
- Profilometer Profilm 3D (Filmetrics)
- Lasercutter (Novograph)
How to get started
If you are interested in utilizing our services, please contact us directly. We can discuss the various methodologies that are available for your project and determine the best technology to meet your specific needs. Each methodology has its own advantages, schedule a meeting to discuss your project and we will help you choose the most suitable technology for the successful completion of your project.
Contact
Sadaf Pashapour, PhD
Facility Manager
IMSEAM
Heidelberg University
Im Neuenheimer Feld 225 (INF 225)
69120 Heidelberg
E-Mail: microfluidics[at]imseam.uni-heidelberg.de
Phone: +49 6221 54 15726